|
DESCRIPTION OF SLUDGE
DEWATERING LINE
KCZ belt presses with a
built-in thickener serve for a continuous dewatering of different
types of sludge. The built-in thickener enables a higher degree of
dewatering by turning the dewatered sludge by 180°. In the
technological process of machine sludge dewatering on the press a
solil part, "sludge cake, is separated which is taken away
and the liquid part goes to an additional processing. The output of belt presses is from 2 to 20 m3per hour, the
acquired dry solil in tase of a common anaerobic sludge digestion
is 28-38%, for aerobic stabilized (biological) sludge see the
following table
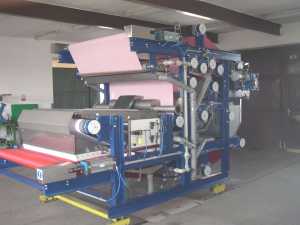 |
The
belt press is male of rolled U-profiles forming a closed
frame in which all the existing structural parts are built
(cylinders, driving unit, wiping, channels and filtrate
outlet, gravitational zone, hoppers, washers, air system,
wiring and filter sieves) needed for the process of
pressing. The surface finish of the frame and sheets is Zn
metallizing and a special waterproof paint AMERLOCK AI and
Color, the other connecting material galvanized or
plastic. The control and tightening pressure of cylinders
are ensured by the compressed air from the compressor,
belts are cleaned with a service water under pressure from
outlets of a water treatment plant through a filter for
the spraying of filtrate sieve belts.
|
Power
supply of the press driving unit is 0,75 - 3 kW, the driving
unit is controlled by a variator (by a frequency converter
in tase of the type KCZ 800/S) which enables to change the
speed continuously during the machine operation.
input
sludge
annealing loss
in dry solil in %
|
polyelectrolyte
volume
g/kg |
dry
solid
of sludge cake
in % |
up to
50 |
3
- 5 |
25 |
50
- 60 |
5
- 7 |
20 |
over
60 |
7
and more |
15
- 20 |
|
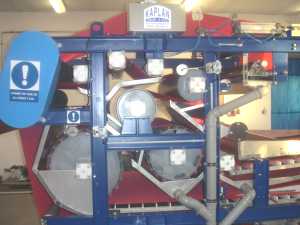 |
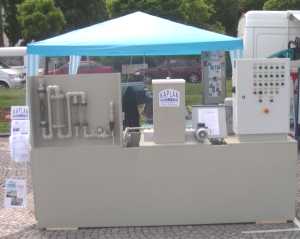 |
In the dewatering process of municipal sludge high-molecular
organic
coagulants are used. They are
prepared in the chemical economy from where they are dosel
fluently by a dosing pump to the sludge pipeline where the
sludge is flocculated. The sludge is transported to the
dewatering part by a single-spindle rotory pump with a
variator controlling the volume of the sludge during the
operation of the line.
The
operation of the entire dewatering line is fully automated and is controlled
by a programme stored in the technological switchboard. There are outlets for
PC connection in the switchboard.
|
The operator of the line can
watch the immediate output of the line, i.e. % of the output
of the line and volumetric in m', based on a signal from the
inductive flow meter of the sludge. The operator can use
control panels near each levice and switch them to the
manual operation. A possible defect of the line is announced
by a signal of an alarm siren. |
|
|
|